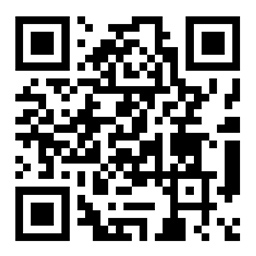
提高我国压力容器制造水平的一项重要改进---实现筒体和封头同步加工,缩短容器生产周期
1. 问题的提出
以前压力容器的生产流程为:外协加工毛边封头,切毛边、加工坡口、测量直边段外圆周长后,筒体下料卷圆,封头和筒体组装。
分析上述流程可知:一、封头厂只提供端部不切边的毛边封头;二、实测封头外圆周长后“才敢”筒体下料制作,两者不能同步加工,以封头和筒体组装的错边 量不超差。其原因是封头的加工技术落后,成形质量差,不能按要求封头的尺寸精度。这就延长了容器的生产周期,是我国容器生产技术与水平存在的差距 之一。
如何创造的条件,满足筒体和封头同步加工的要求,以缩短生产周期,适应我国加入WTO后面临的挑战,缩小与水平的差距,是我国容器界封头行业努力解决的课题之一,具有明显的经济价值和现实意义,其关键是提高我国的封头制造质量。
近年来,由于宜兴北海封头有限公司引进了日本北海的封头制造技术,使我国的封头制造向化发展,按严于标准的内控质量标准组织生产,大地提高了我国的封头质量,了尺寸精度,为筒体和封头同步加工创造了的条件。
为了适应技术进步和生产发展的需要和可能,由压力容器标准化委员会制造分委员会制订的《钢制压力容器用封头》标准(以下简称《新封头标准》)中的有关技术要求,就是以筒体和封头可同步加工这一基点提出的。
现根据筒体和封头同步加工应具备的条件,并对照《新封头标准》的技术要求进行分析。